Ditch the paperwork, keep track of all your work orders seamlessly.
Generate, track, and manage work order from initial requests to completion.
Sign Up for Free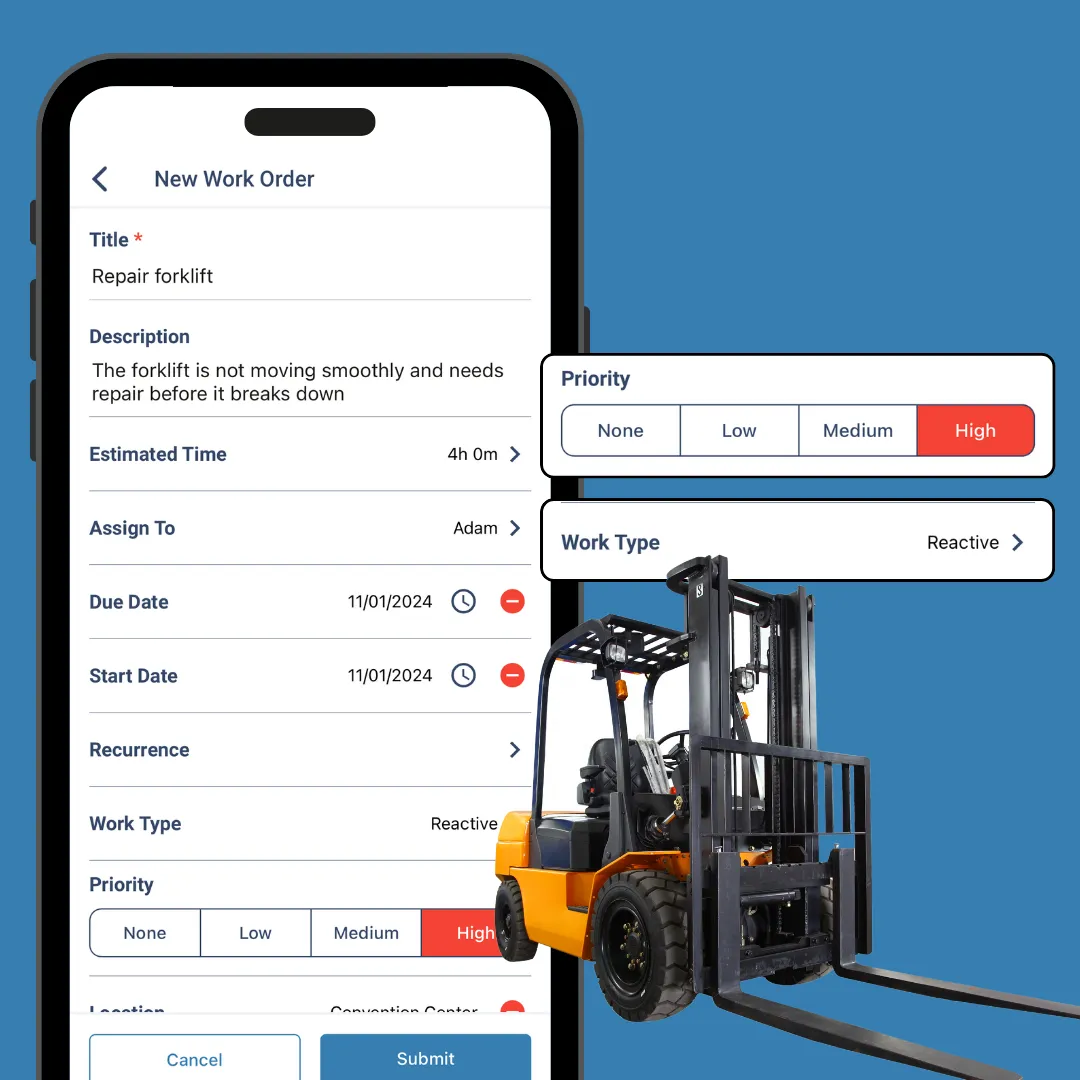
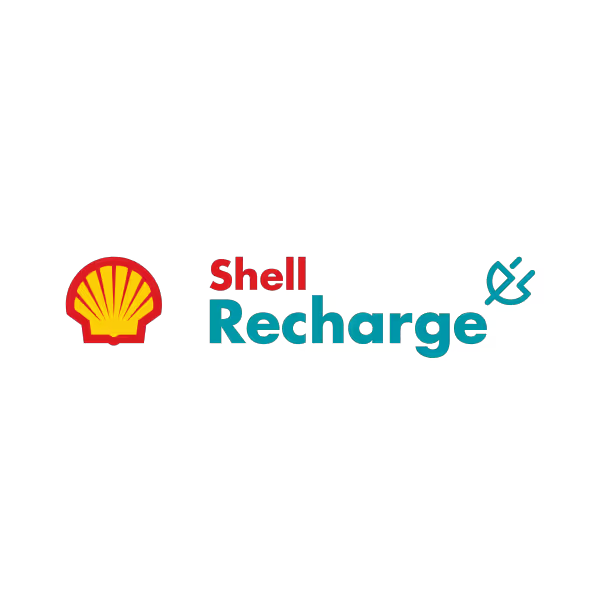
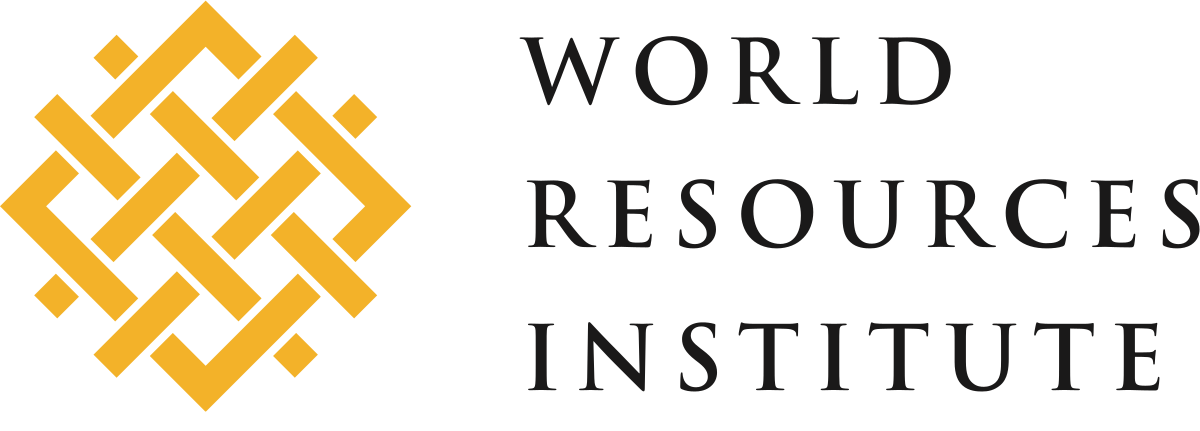
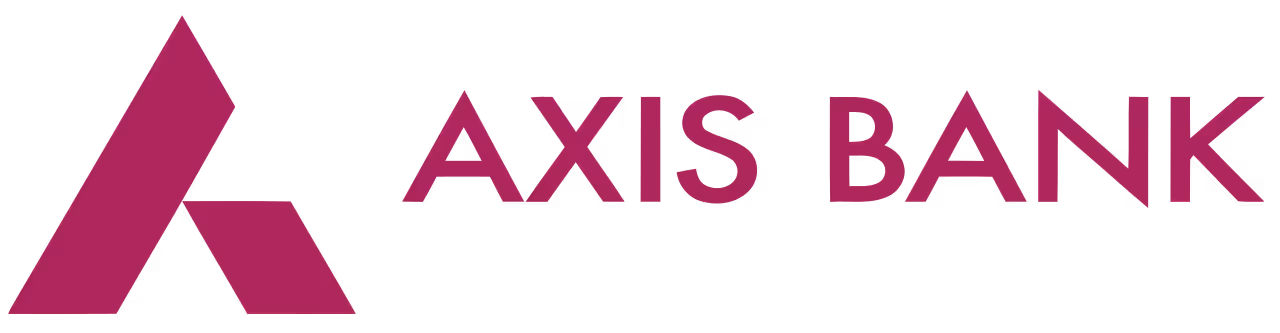
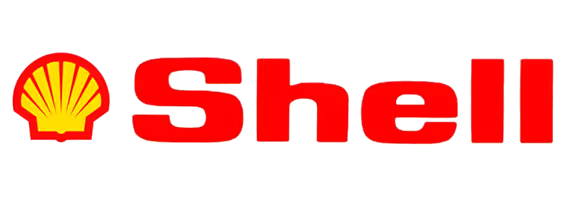
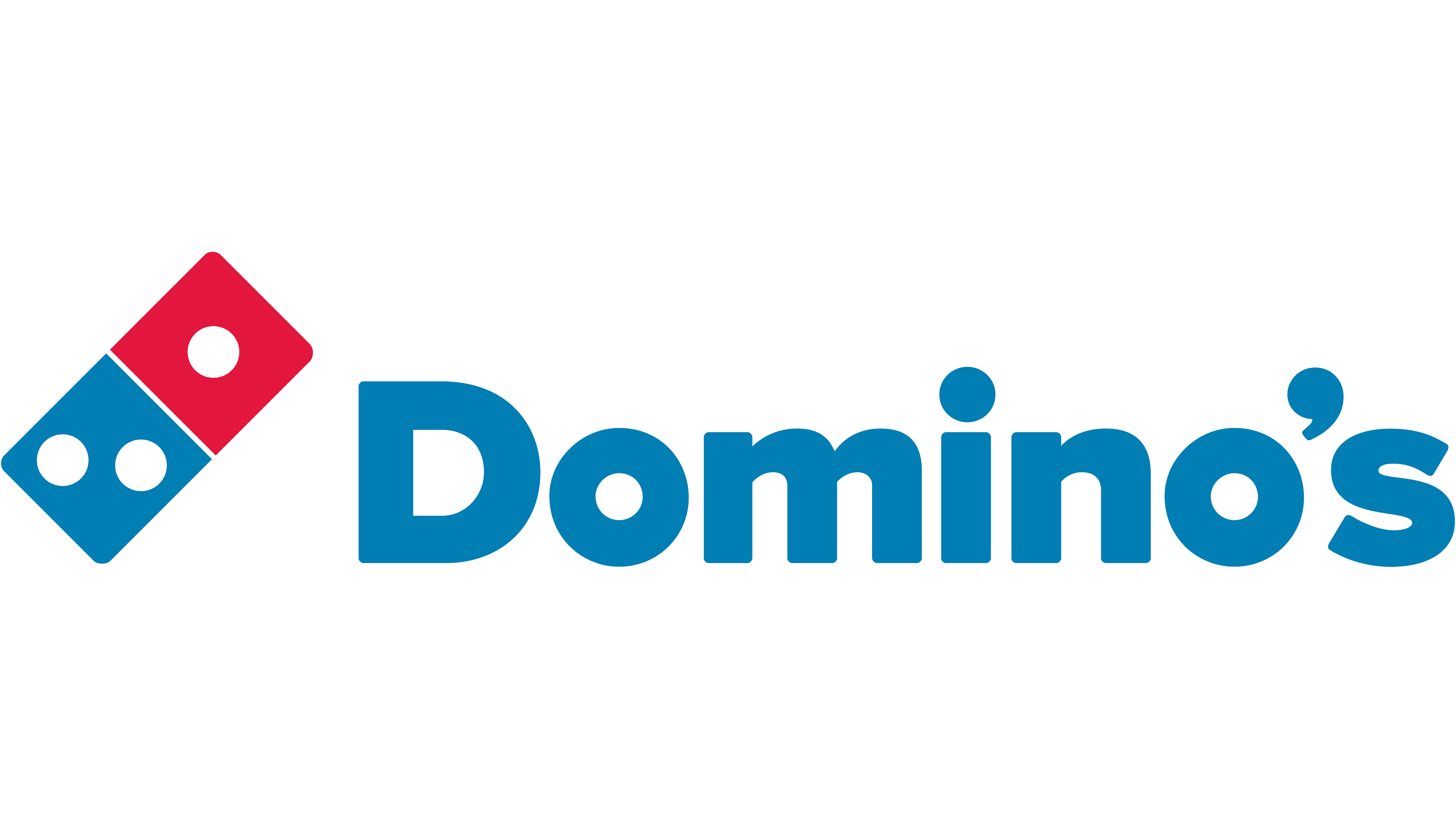
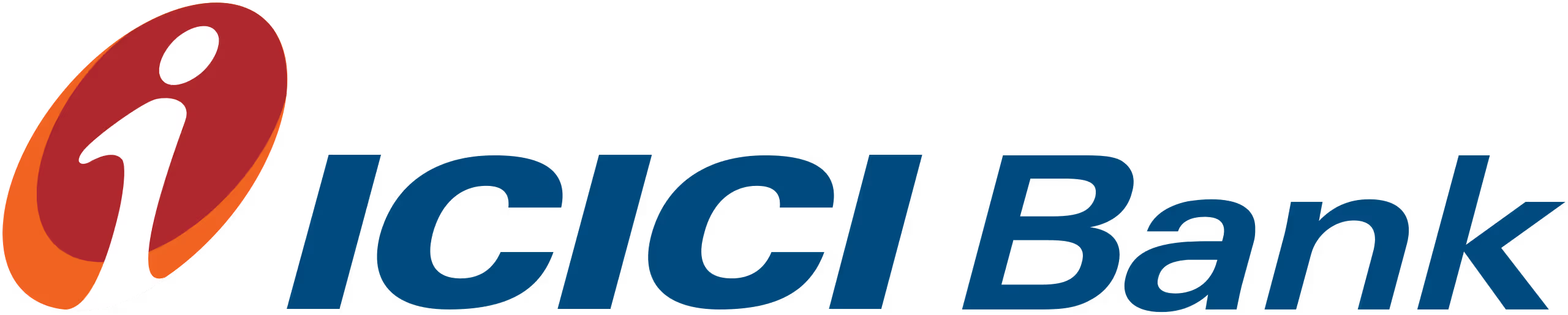
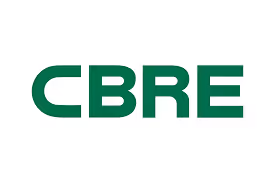
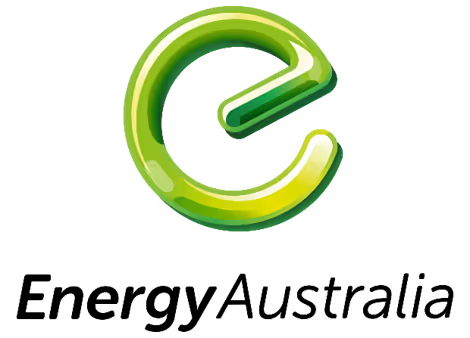
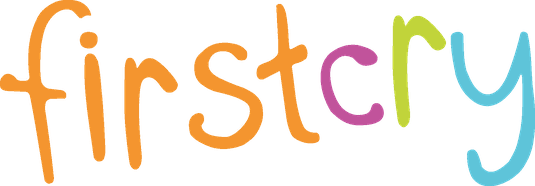
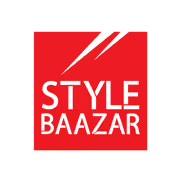
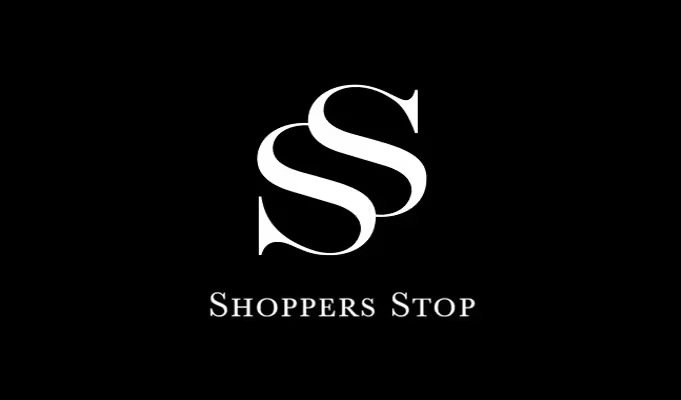
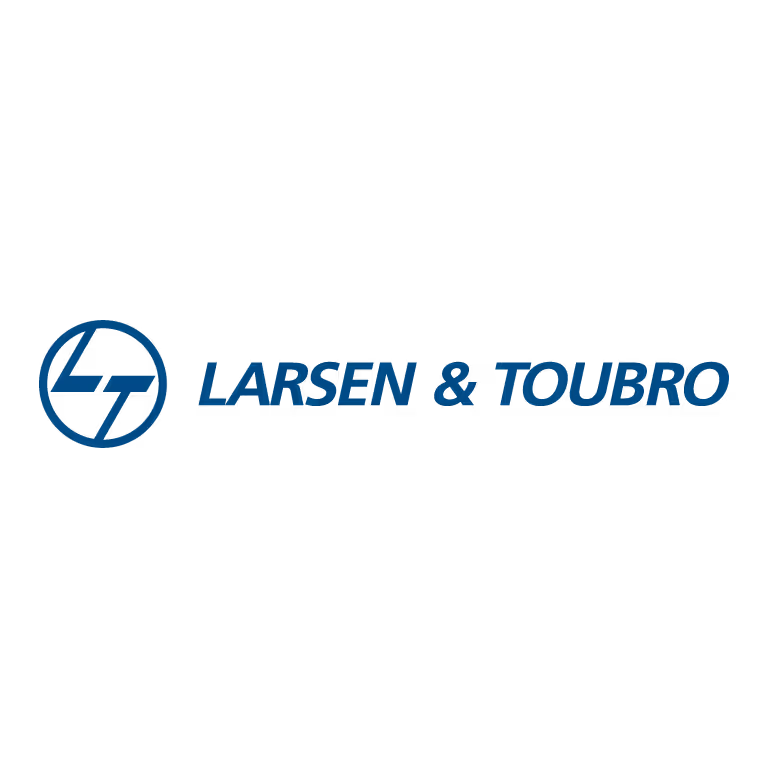
Improve Workflows, Prioritize Tasks, & Increase Realiability
Easily generate work orders for both preventive maintenance and corrective repairs. Work orders can be assigned to specific technicians or teams, ensuring accountability, and that maintenance tasks are organized, tracked, and completed efficiently, minimizing downtime and improving asset performance.
Get Started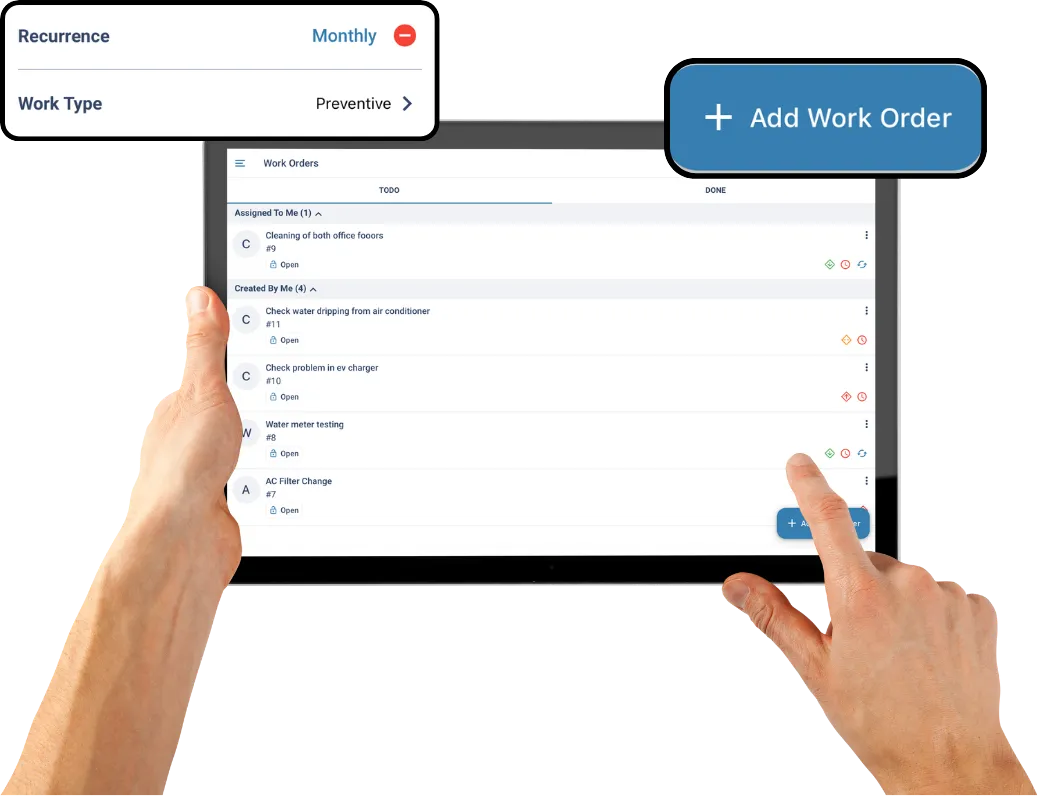
We have some features that we think you would fall in love with!
Set priority levels (e.g. high, low) and custom statues (e.g. in progress, done) for work orders. Enable technicians and managers to add notes, photos, or comments directly to work orders, improving communication and ensuring that all necessary details are available in one place.
Get Started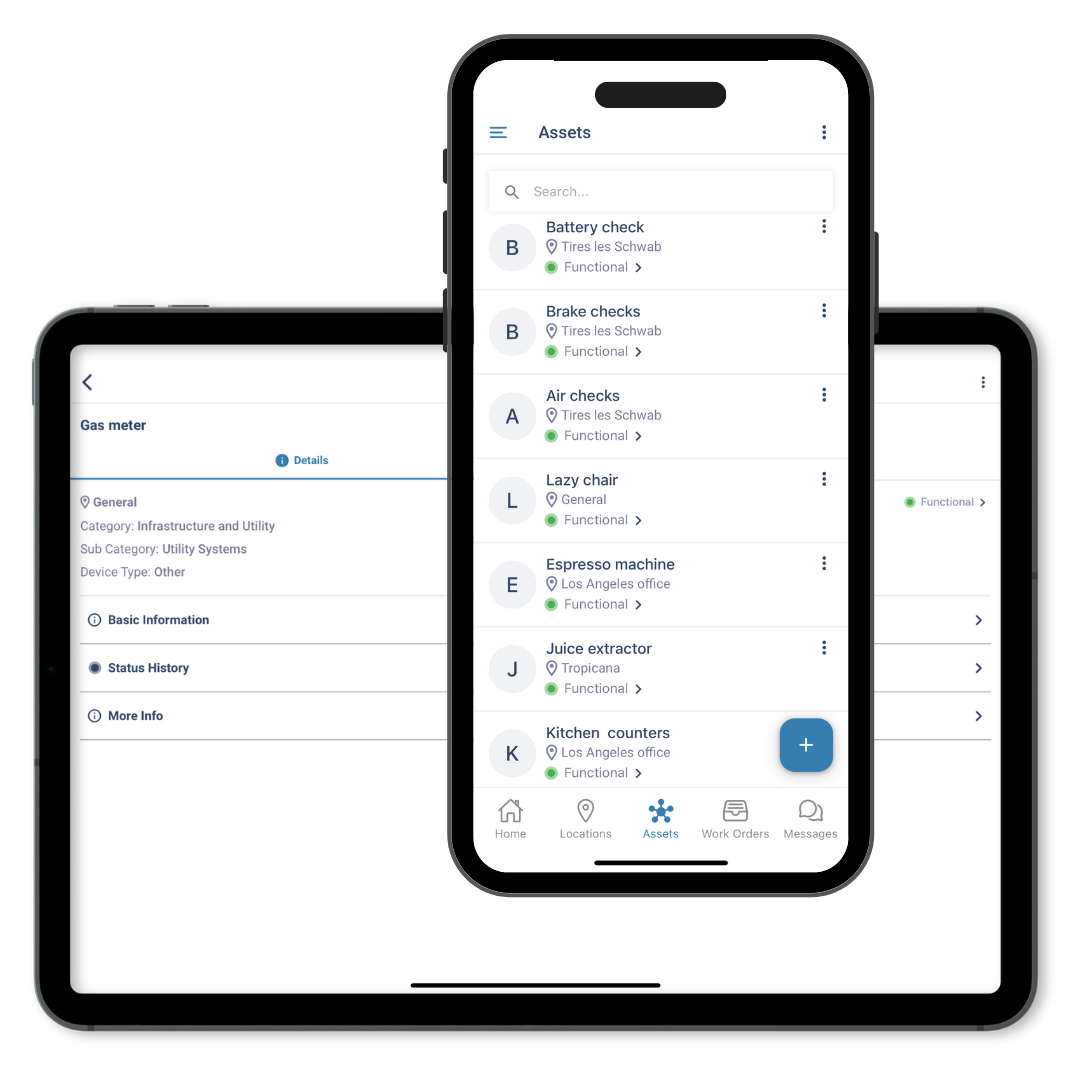
Work Order History
Keep a detailed log of all completed work orders for each asset, including technician notes, parts used, time taken, and costs. This provides valuable data for audits, future maintenance planning, and asset performance analysis.
Progress Monitoring
Track the real-time status of work orders from start to completion. Users can monitor task progress, ensuring that work is completed on time, and receive notifications for overdue or high-priority tasks.
Mobile Access
Technicians can access, update, and close work orders from mobile devices, enabling real-time management and reducing delays in field operations.
Assignment & Scheduling
Work orders can be assigned to specific technicians or teams, ensuring accountability. CMMS also allows scheduling based on technician availability and task priority, optimizing workforce management.
Less Paper, More Productivity
The Energos platform helps businesses digitize workflows and start their data journey.
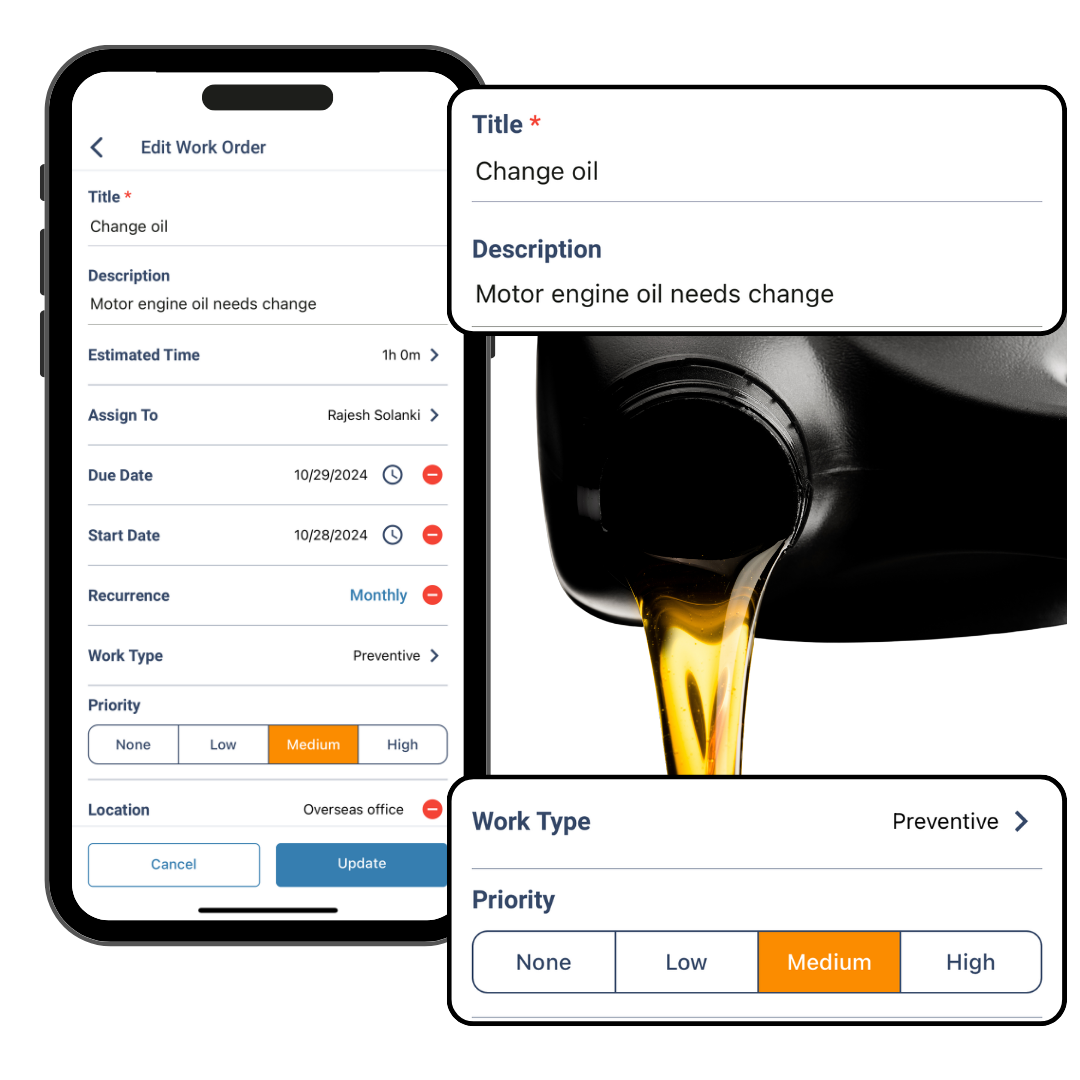
Recurring Work Orders
Recurring work orders help ensure that routine maintenance, such as inspections, lubrication, or filter replacements, is performed consistently without the need for manual scheduling. By automating these tasks, organizations can prevent equipment breakdowns, improve asset reliability, and maintain a smooth workflow, reducing downtime and extending the lifespan of machinery.
Get Started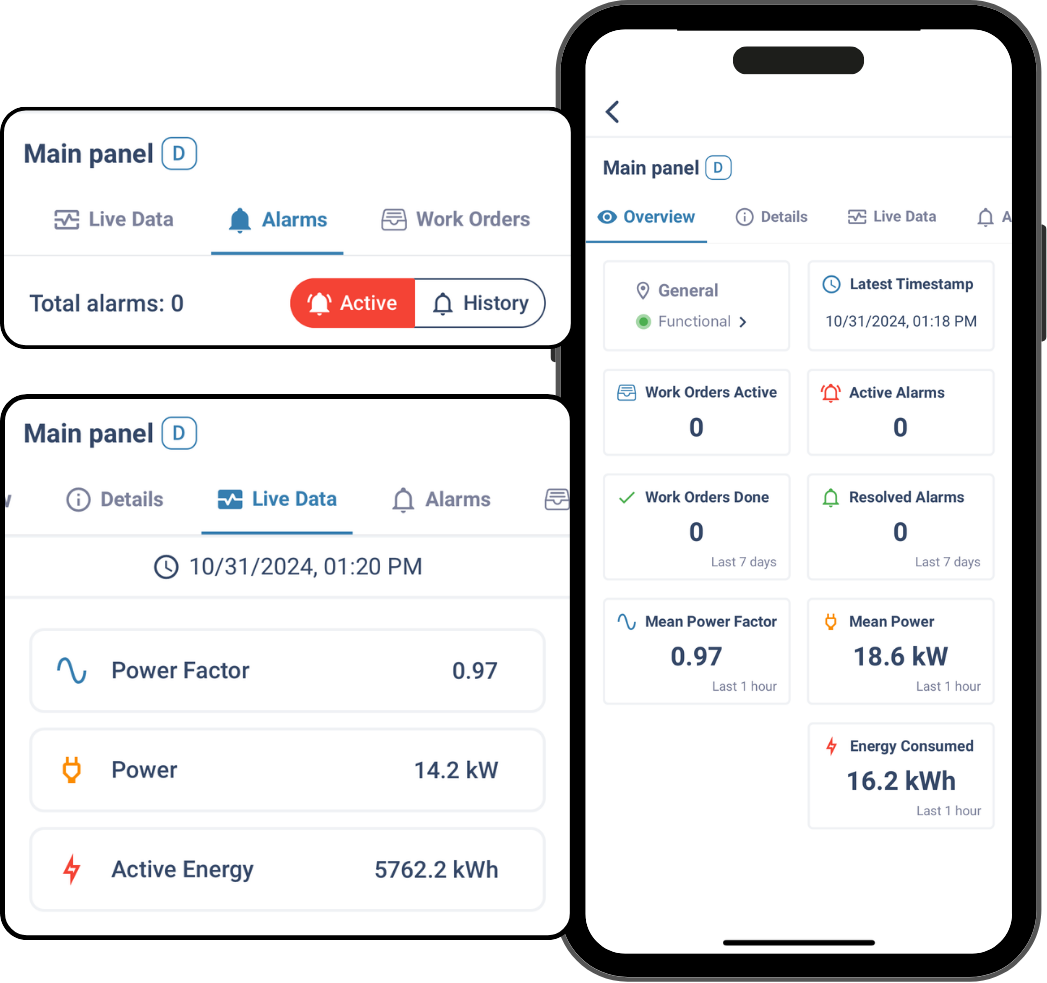
IoT Integrations
IoT (Internet of Things) enhances work order management by providing real-time data from connected devices and sensors on equipment. When IoT detects an issue—such as abnormal temperature, vibration, or usage—it can automatically trigger a work order in the maintenance system. This enables proactive maintenance, ensuring issues are addressed before they lead to equipment failure. By integrating IoT with work orders, organizations can optimize maintenance tasks, reduce downtime, and improve asset performance with data-driven insights.
Get started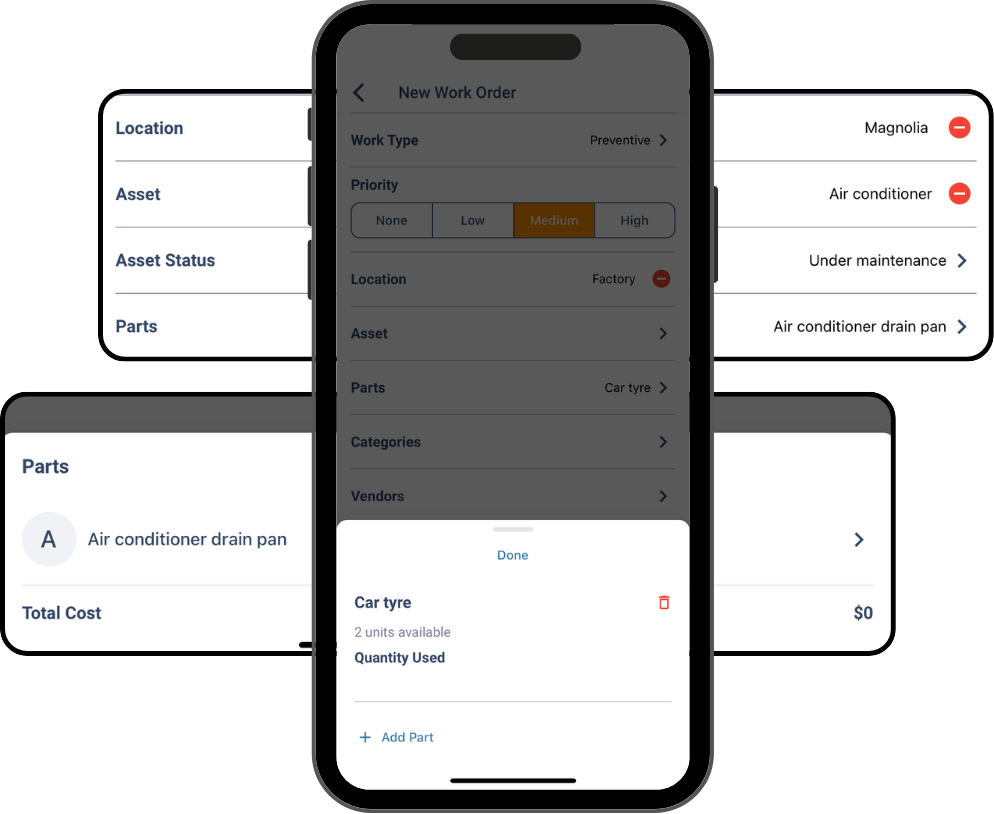
Resource & Inventory Management
Link required tools, parts, or materials to each work order. This ensures that technicians have everything they need to complete the job, reducing downtime caused by missing resources.
Get Started