Enhancing Energy Efficiency & Maintenance for McDonald's
McDonald's struggled with rising energy costs and frequent maintenance issues, from HVAC inefficiencies to fryer malfunctions and signage failures. Energos introduced IoT-driven monitoring, smart meters, and automated work orders, cutting energy consumption by over 15% and minimizing downtime. See how smart facility management transformed operations for one of the world's largest QSR brands.
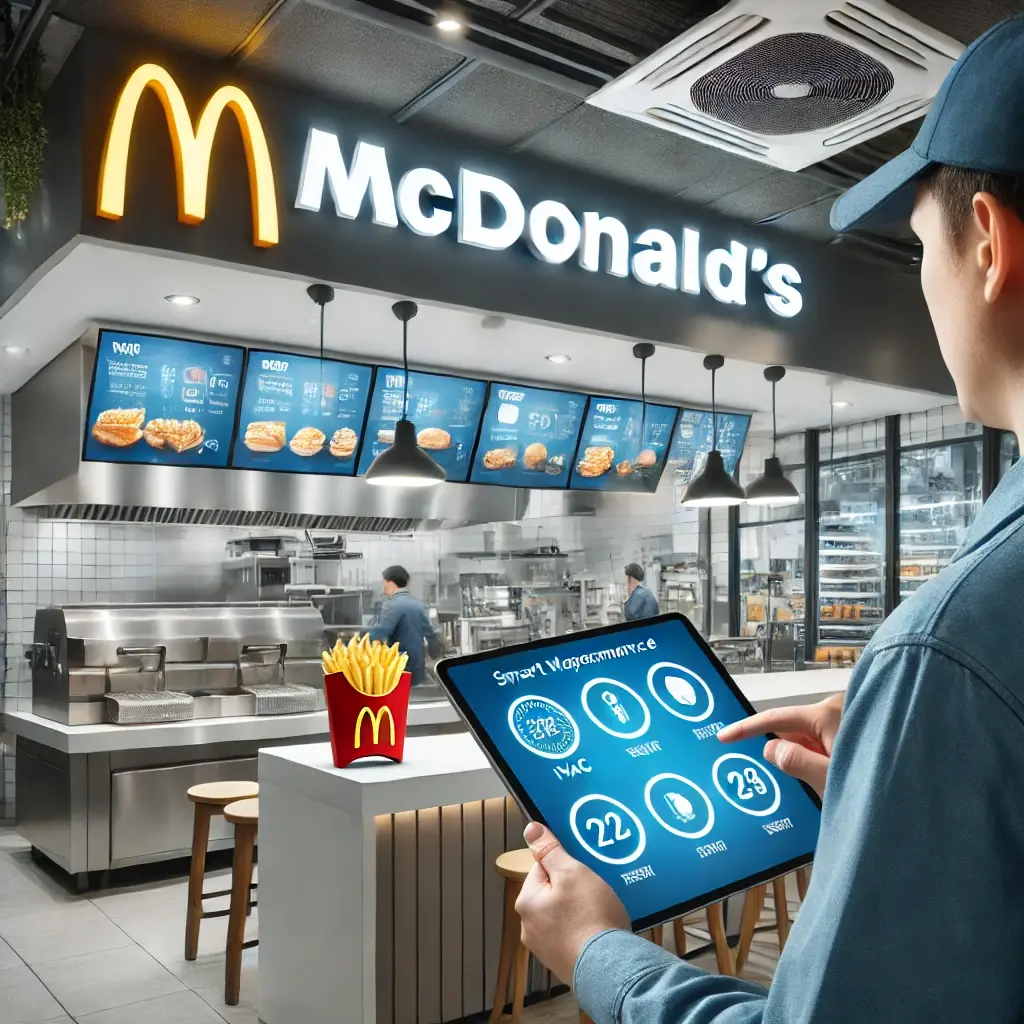
Client: McDonald's
Industry: Quick-Service Restaurants (QSR)
The Challenge:
McDonald's faced rising energy costs across multiple outlets while striving to maintain optimal in-store temperature conditions for customer satisfaction. Additionally, their maintenance teams struggled with:
- HVAC System Performance Issues: Difficulty in assessing whether HVAC units were underperforming, leading to inefficiencies.
- Frequent Signage Lighting Failures: Recurrent emergency repair requests for external signage lighting.
- Fryer Downtime: One of the two fryers in many outlets frequently malfunctioned, requiring urgent vendor intervention.
These issues led to increased operational costs, frequent repair emergencies, and inconsistent equipment performance.
The Solution Implemented:
Energos provided an IoT-driven solution to optimize energy management and streamline maintenance operations:
- IoT-Powered HVAC & Room Condition Monitoring
- Installed sensors to track HVAC efficiency and detect performance deviations.
- Maintained optimal room conditions while reducing unnecessary energy usage.
- Smart Meter Integration for Fryer Monitoring
- Implemented smart meters to monitor fryer operation times through real-time current flow data.
- Identified downtime patterns and proactively scheduled maintenance before critical failures.
- Automated Work Order Management through CMMS
- Digitalized maintenance requests and repair logs.
- Enabled maintenance staff to track service history, reducing emergency breakdowns.
The Results & Impact:
- Over 15% Reduction in Energy Costs by eliminating time leakages in after-store hours.
- Improved HVAC Efficiency with data-driven monitoring and maintenance.
- Reduced Emergency Repairs by proactively tracking signage lighting and fryer performance.
- Minimized Downtime with better vendor coordination and predictive maintenance.
By leveraging IoT-powered analytics and workflow automation through CMMS, McDonald's successfully optimized energy consumption and improved equipment reliability. This case study highlights how smart facility management can enhance operational efficiency and cost savings in the QSR industry.Want to reduce energy costs and streamline maintenance operations? Get in touch with Energos today!