Shell's Digital Transformation in Maintenance with IoT
Shell leveraged IoT driven maintenance to transform its 200+ fuel stations and convenience stores, integrating real-time monitoring for fuel systems, power infrastructure, and HVAC. By automating alarms, predictive maintenance, and energy optimization, the expected project outcome is reduction in emergency site visits by 50% and shifting of operations from reactive to preventive maintenance. Discover how IoT powered insights improved efficiency, cost savings, and customer experience.
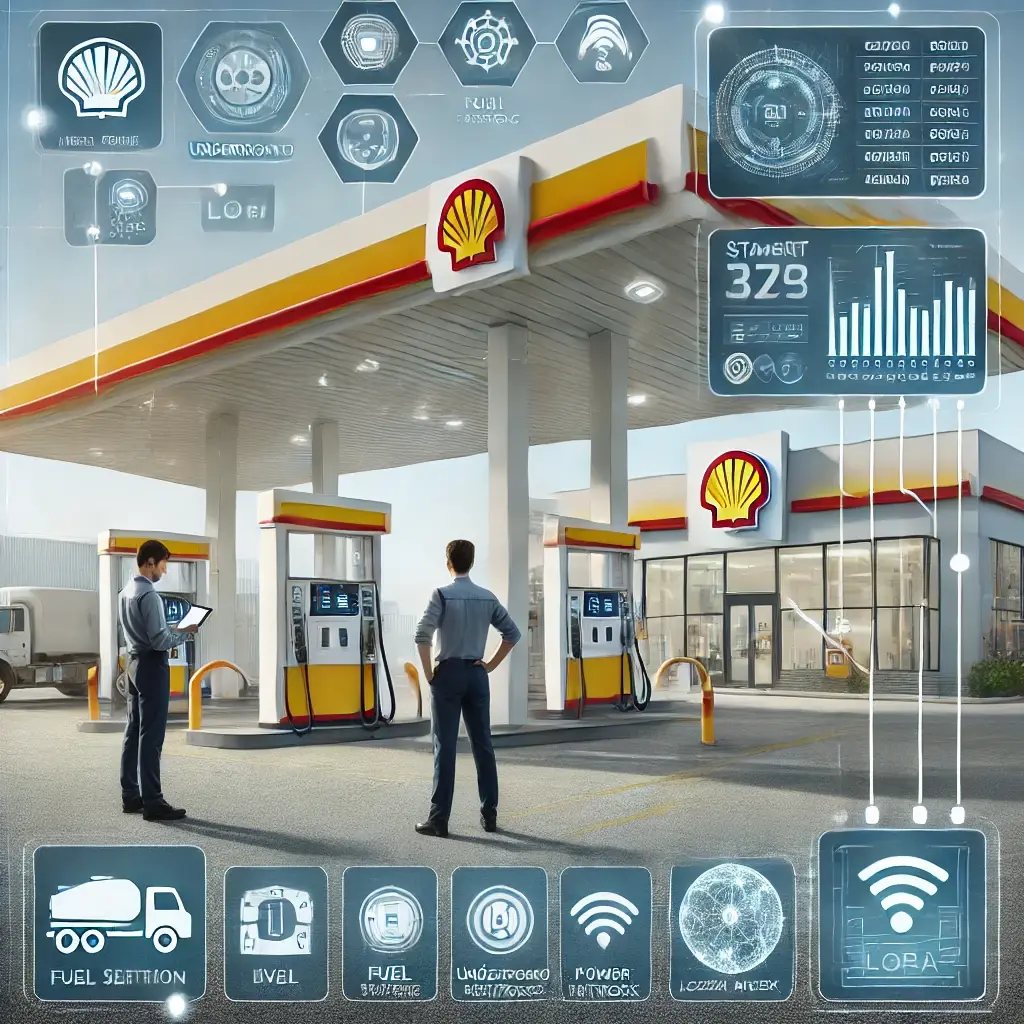
Client: Shell
Industry: Fuel Retail & Convenience Stores
The Solution: IoT Powered Digital Maintenance & Asset Monitoring
The Challenge:
Shell aimed to digitalize its maintenance operations by leveraging IoT generated alarms, notifications, and action workflows. The project required integrating real-time monitoring of equipment across 200+ fuel stations and convenience stores, each with over 20 critical assets. The key challenges included:
- Fuel System Monitoring: Dispensers, DHIB, Vapor Recovery Systems, VFC, and ATG based underground tank monitoring.
- Power System Monitoring: Water meters, electrical smart meters, power panels, battery backups, and UPS condition monitoring.
- HVAC & Cold Chain Monitoring: Chillers, freezers, and HVAC systems in convenience stores for temperature compliance and energy efficiency.
- Data Security & Compliance: Ensuring SOC2 compliance, encrypted wireless (LoRa Mesh) connections, and adherence to strict data privacy norms.
- Reducing Reactive Maintenance: Shifting from reactive to predictive & preventive maintenance with automated work orders and real-time alerts.
The Solution Implemented:
To address these challenges, a fully integrated IoT enabled maintenance system was deployed, incorporating:
Wireless IoT Sensors & LoRa Mesh Connectivity
- Installed across fuel stations, power systems, and convenience stores to ensure 24/7 data collection.
- Real-time condition monitoring of fuel dispensers, electrical infrastructure, HVAC, and refrigeration units.
Automated Alarms & Workflows
- IoT generated alarms and notifications trigger actionable insights.
- Predictive maintenance alerts based on equipment performance trends.
- Customizable reporting & dashboards to analyze maintenance KPIs.
Energy Efficiency Optimization
- HVAC control automation for energy cost reduction.
- Smart energy monitoring via electrical meters and power backups.
- Reduced unnecessary power consumption across Shell’s convenience stores.
Data Security & Compliance
- SOC2 certified architecture ensuring secure data handling.
- Encrypted wireless connectivity for data protection.
- Role based access controls to protect operational data.
The Results & Business Impact:
1. 50% Reduction in Emergency Site Visits
2. Shift from Reactive to Preventive Maintenance
3. Significant Energy Cost Savings via HVAC Optimization
4. Enhanced Data Driven Decision Making with Reports & Predictive Models
5. Streamlined Maintenance Operations for Better Consumer Experience
By implementing IoT driven condition monitoring, Shell successfully minimized manual interventions, improved operational efficiency, and ensured proactive maintenance—all while optimizing costs and enhancing consumer service quality.
Future Scope
The next phase of this project includes AI powered predictive maintenance, deeper analytics for failure prevention, and further integrations with Shell’s enterprise systems.
Looking to transform your maintenance operations with IoT? Get in touch with us today!